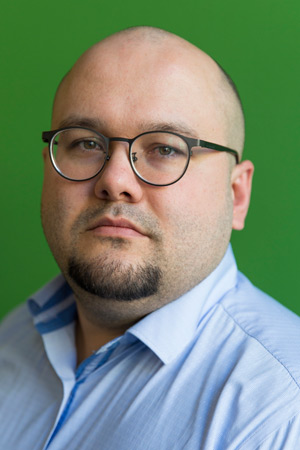
Антон Шаронов, главный технолог
SharonovAA@dipaul.ru
Современные предприятия все меньше зависят от ручного труда. Высокотехнологичные решения приводят к сокращению работников и увеличению использования эффективных машин, а точное литьевое производство сейчас немыслимо без аддитивных технологий и 3D-оборудования.
Сегодня, например, для получения точных изделий в кратчайшие сроки применяется технология литья по выжигаемым и выплавляемым моделям. Предлагаем краткий обзор применения аддитивных решений в таком направлении, как «Литье по выплавляемым и выжигаемым моделям».
Варианты получения мастер-модели
QuickCast (QC) — быстрое литье
Данное решение связано с технологией стереолитографии (SL), позволяющей создавать высокоточные полые изделия с сетчатой структурой. Один из наиболее популярных способов, служащих для получения как выжигаемых моделей, так и мастер-моделей. Хорошее качество поверхности и высокая точность моделей, экономичность процесса делают востребованной эту технологию. За счет сетчатой структуры QC не оказывает давления на стенки формы при выжигании. Кроме того, благодаря сетчатой структуре расходуется в несколько раз меньше материала относительно реального объема детали, что позволяет успешно применять QC и при литье в гипс.
Рис. 1. Образец сетчатой структуры QC
Отверждение светом (dlp и аналоги)
Один из вариантов SL-технологии (аналог QC). При работе применяется фотополимер, отверждаемый с помощью света (волны разной длины). Многие компании разрабатывают специальные материалы для dlp с возможностью легкого выжигания. В связи с высокой ценой материала технология чаще используется при выжигании объектов небольшого размера (стоматология, ювелирное производство и т. п.).
Впрыскивание материала (material jetting, MJ)
По технологии MJ материал подается на платформу из печатающий головки с большим количеством сопел (по аналогии со струйной печатью обычного принтера). Позволяет с хорошей скоростью получать точные изделия. Технология наиболее популярна при производстве небольших изделий (стоматология, ювелирное производство и т. п.).
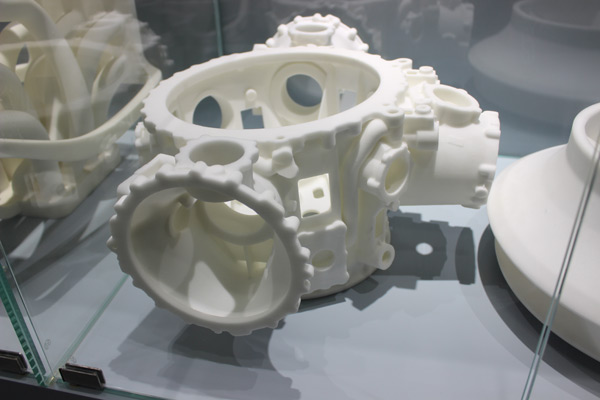
Рис. 4. Пример изделия, построенного по технологии SLS PS
Лазерное спекание (SLS)
При селективном лазерном спекании происходит спекание мелкодисперсного порошкового материала с помощью лазера. SLS-машина использует полистирол, который чаще всего пропитывается воском. Данная технология не позволяет обеспечить высокое качество поверхности и точность, но характеризуется невысокой стоимостью и возможностью построения больших объектов.
Струйная печать (Voxeljet)
Своеобразный гибрид MJ- и SLS-технологий, когда деталь формируется по принципу струйной печати, а затем пропитывается восковым составом. Детали, полученные с помощью данной технологии, называют полиметилметакрилат (ПММА).
Итак, мы рассмотрели варианты получения мастер-модели, применяемой при литье металлов по выплавляемым выжигаемым моделям. Существуют и другие технологии (например, производство форм для прямой заливки или получения частей форм оснастки), но это тема следующей статьи.
От теории — к практике
«Диполь» является поставщиком 3D-оборудования для разных областей промышленности. В задачи компании входит не только поставка, пусконаладка, обучение персонала и сопровождение при работе с 3D-оборудованием, но и производственный аудит промышленной пригодности аддитивных решений в компании заказчика. Рассмотрим использование нашего 3D-оборудования на одном из предприятий для получения высокоточной отливки из алюминия по выжигаемой модели QC (SLA-технология компании Shining 3D, ведущего разработчики и производителя в направлении 3D-печати и сканирования, а также крупнейшего поставщика услуг по прототипированию).
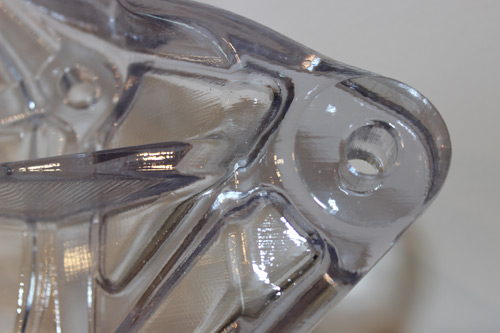
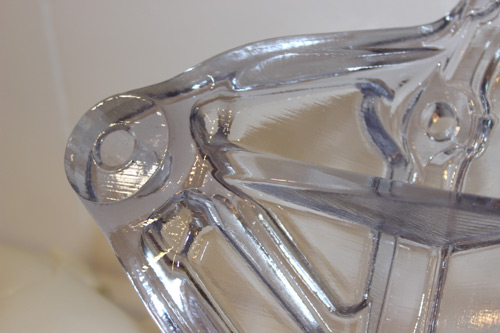
Рис. 5. Изделие из материала Somos WaterShed 11120
Образцы для проведения испытаний были получены на SLA-принтере SH3D iSLA-450 PRO (зона построения 450×450×350 мм). Данная машина, оснащенная немецкой системой сканирования ScanLab, американским лазером и японской электроникой, позволяет с легкостью выполнять необходимые по качеству функциональные модели. Кроме того, широкий выбор материалов для этой машины позволяет получать детали с такими важными характеристиками, как термостойкость (до 268°), эластичность, повышенная прочность. В последнее время все чаще находят применение и биосовместимые материалы. Благодаря вышесказанному, стереолитографический 3D-принтер iSLA-450 PRO нашел применение практически во всех известных отраслях — автомобилестроении, авиастроении, приборостроении, кораблестроении, медицине, дизайне, маркетинге и многих других сферах деятельности. В нашем случае использовался Somos WaterShed 11120 (производства компании Dutch State Mines, DSM) — полупрозрачный материал, разработанный специально для получения прототипов (в том числе характеризуется низкой зольностью). Характеристики материала приведены в таблице 1.
Таблица 1. Характеристики материала Somos WaterShed 11120
Параметр | Значение |
---|---|
Предел прочности при разрыве | 47,1–53,6 MPa |
Удлинение при разрыве | 11–20% |
Модуль упругости | 2,650–2,880 MPa |
Предел прочности при изгибе | 63,1–74,2 MPa |
Модуль упругости при изгибе | 2,040–2,370 MPa |
Водопроницаемость | 0,35% |
Плотность | ~1,12 g/cm3 @ 25 °C |
Вязкость | ~260 cps @ 30 °C |
Дополнительно | Оптическая прозрачность |
Для изготовления выбрана несложная деталь с условным названием «крышка насоса». Было решено изготовить четыре образца с различными усадками под алюминий (для двух образцов была заложена усадка 1,8%, для двух дргуих — 2,4%.).
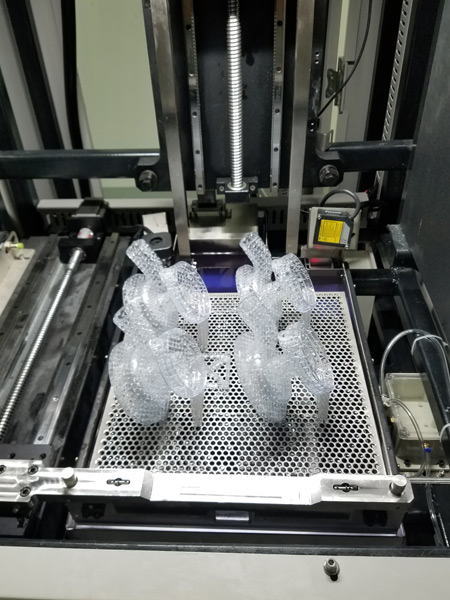
Рис. 6. Крышка насоса (QC)
Сначала детали были напечатаны, что заняло около 6 ч. На рис. 7 показаны напечатанные образцы. Точность напечатанных изделий составила 0,1 мм.
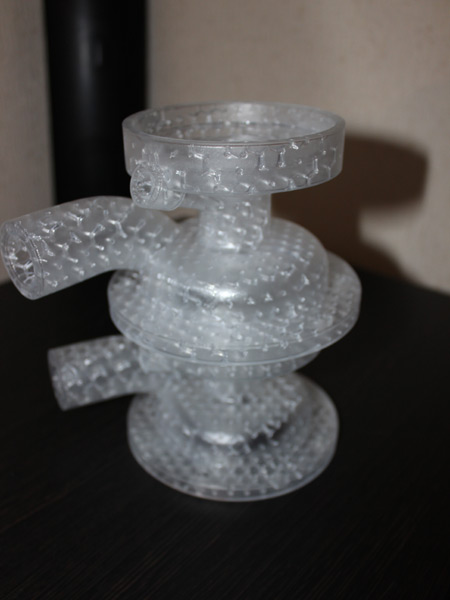
Рис. 7. Крышка насоса (QC) — два образца
Далее детали промыли, продули воздухом через специальные технологические отверстия для удаления остатков материала, затем на 40 мин поместили в печь дополимеризации, чтобы придать им большую прочность. После этой процедуры готовые детали передали на литьевое производство для напайки на так называемое «дерево».
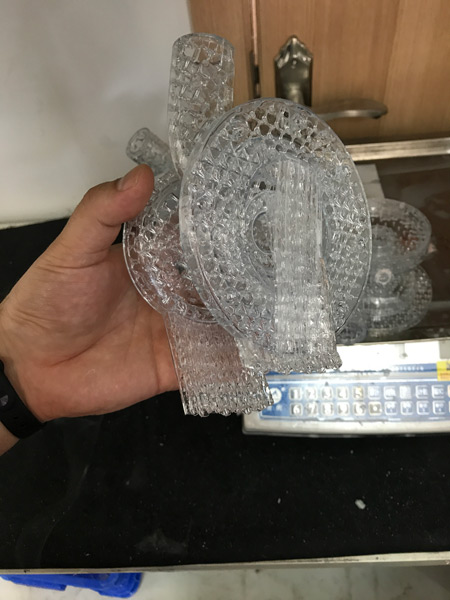
Рис. 8. Отмытый образец с поддержками
Процесс создания формы осуществляется по стандартным технологиям, описание которых можно опустить. Следует указать, что необходимо запаять все технологические отверстия (для этого предпочтительна смола с использованием УФ-устройства или восковая смесь).
Затем литниковая система припаивается к детали и крепится на стояк. В порядке эксперимента мы позволили себе использовать один стояк для одной детали. Применяемая оболочковая форма состояла из кварцевого песка и связующего состава на водной основе.
Дальнейший стандартный процесс литьевого производства состоит из следующих этапов:
- напайка литников и питателей (рис. 9);
- создание литниковой системы (рис. 10);
- создание первых слоев оболочковой формы (рис. 11);
- сушка формы (рис. 12);
- передача полученной формы на последующее выжигание (рис. 13).
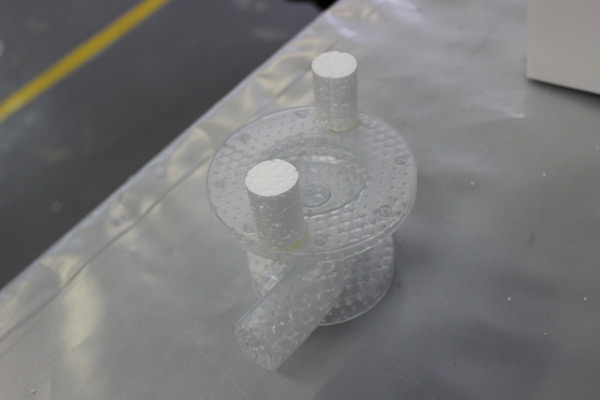
Рис. 9. Напайка литников и питателей
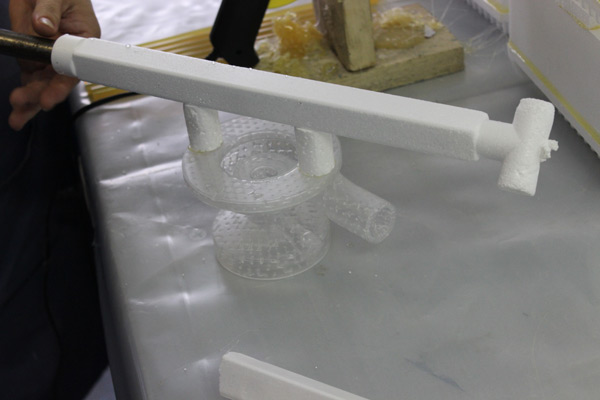
Рис. 10. Создание литниковой системы
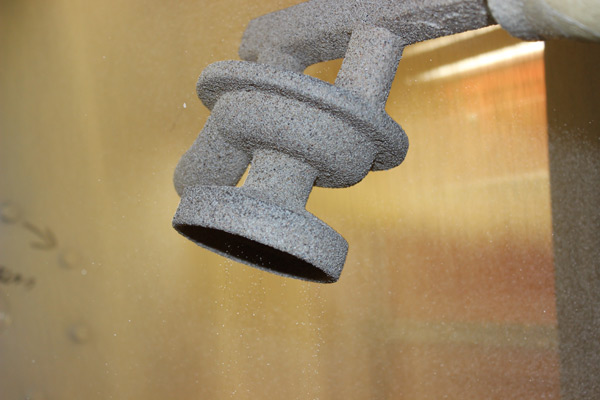
Рис. 11. Создание первых слоев оболочковой формы
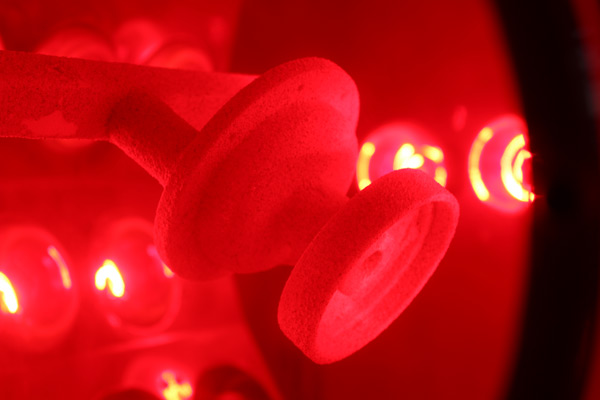
Рис. 12. Сушка формы
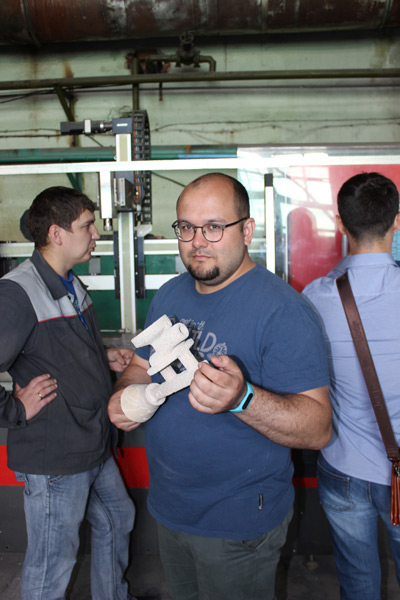
Рис. 13. Передача полученной формы на последующее выжигание
Выжигание модели — один из наиболее важных процессов. При этом следует максимально сократить время операции, чтобы исключить повреждение формы и обеспечить равномерное и полное выжигание материала. Для исполнения этих требований есть несколько рекомендаций. Важно помнить, что при изготовлении крупногабаритных деталей необходимо создавать технологические отверстия для удаления газов. Впрочем, эту процедуру можно проводить и при работе с небольшими деталями. Поскольку существует много факторов, влияющих на качество корки и зольность (общий объем, толщина стенок, плотность внутренней сетчатой структуры и т. д.), каждое производство со временем вырабатывает свои режимы работы. Считается, что оптимальной для выжигания фотополимера является температура 815–1000 °С. Зарубежные производители рекомендуют использовать автоклав, так как он дает более качественный и стабильный результат при небольших временных затратах. В нашем случае была печь с терморегулятором, при этом применялся так называемый полочный режим выжигания, с нагревом и без охлаждения (рис. 14).
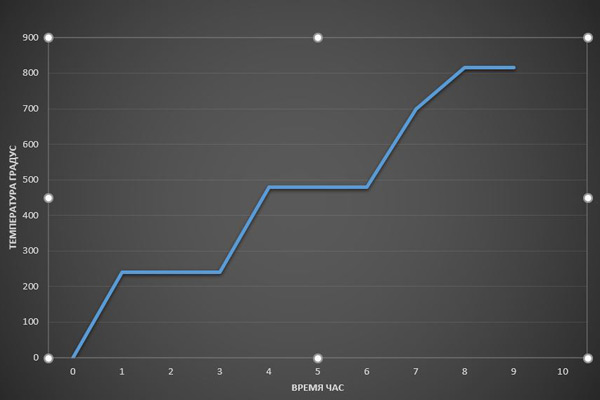
Рис. 14. Схема выжигания
Существуют разнообразные режимы выжигания. Каждое производство определяет выбор конкретного режима, исходя из имеющихся технологий. Например, при использовании быстрого режима выжигания необходимо создать технологические отверстия для газоотведения. Мы использовали программируемую печь с длительным технологическим режимом (более 9 ч). Параллельно создаем еще пару оболочковых форм для работы. По технической спецификации наш материал обладает очень низкой зольностью (график технической спецификации демонстрирует зольность ниже 0,1%, рис. 15).
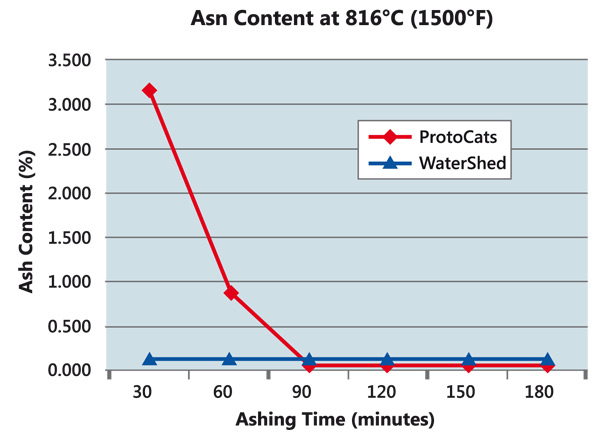
Рис. 15. График технической спецификации фотополимера
При разломе формы можно убедиться в действительной зольности (рис. 16, 17).
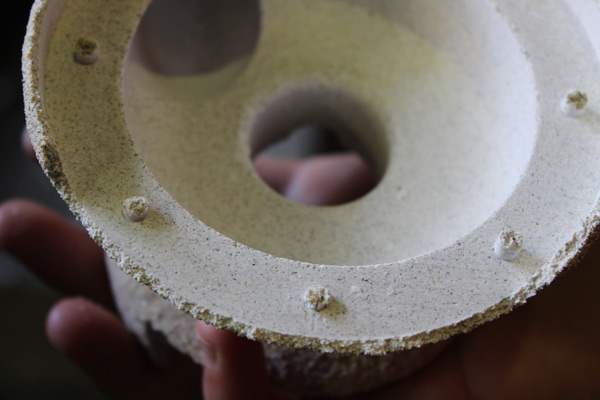
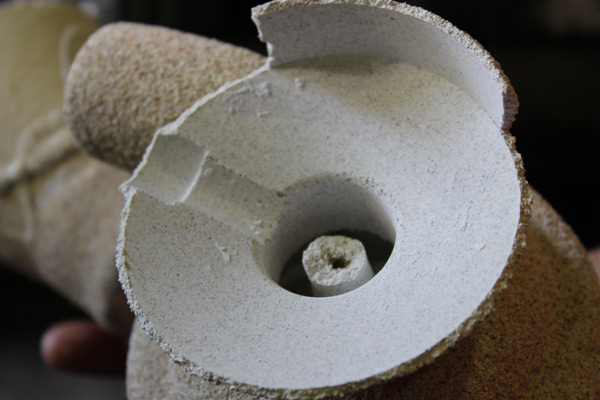
Рис. 16, 17. Минимальная зольность оболочковой формы
Как видно на фото, зольность действительно незначительная, поэтому на дальнейших этапах от ее остатков можно легко избавиться продуванием воздухом. Возможность уже на этапе отливки создать шероховатость меньше 3 мкм по Ra в некоторых ситуациях позволяет получать конечное изделие без дальнейшей постобработки. На рис. 18, 19 видно качество формы, которое можно получить при использовании надлежащих материалов и оборудования.
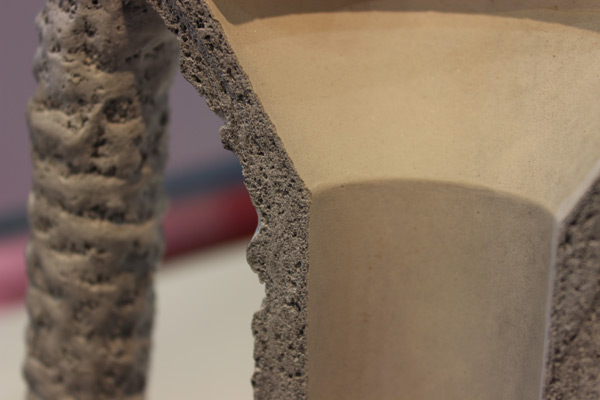
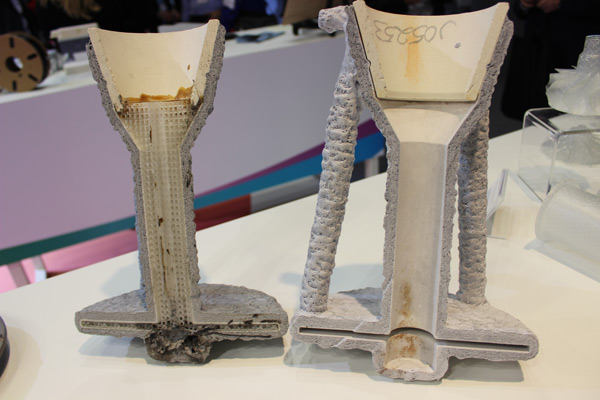
Рис. 18, 19. Оболочковая форма с высоким качеством поверхности
После выжигания образца форма отдается в прокалку и подготовку для заливки алюминия (заливка производится в разогретую форму).
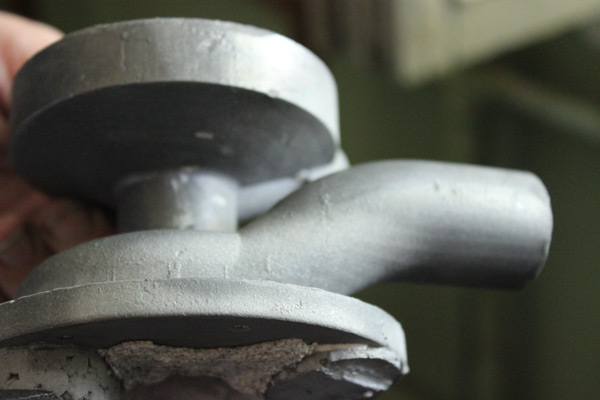
Рис. 20. Отливка из алюминия
Полученную отливку необходимо сравнить с полученной 3D-моделью (без усадочного коэффициента). Для этого используется лазерный ручной 3D-сканер FreeScan X7. Трехмерное оборудование позволяет меньше чем за 1 ч получить информацию о поле отклонений, что очень удобно для понимания, по какому квалитету была получена отливка.
Подводя итоги проведенной работы, можно отметить следующие преимущества SLA-технологии (Shining 3D) и модели QC:
- Скорость. Готовую отливку из металла можно получить уже через 3–4 дня, что существенно сокращает дальнейший цикл создания изделия, позволяя в сжатые сроки перейти к его испытаниям, после чего либо внести необходимые правки, либо отправить изделие в тираж.
- Точность. Высокоточные промышленные 3D-принтеры позволяют получать отливки с очень высокой точностью, в нашей ситуации — третий квалитет точности (ГОСТ 26645-85).
- Качество поверхности внутренних каналов. Шероховатость конечной отливки составляет меньше 3 мкм по Ra, что позволяет избежать механической обработки в сложнодоступных местах.
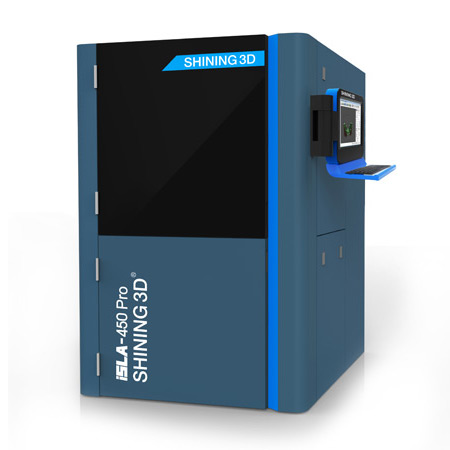
Рис. 21. Промышленный 3D-принтер iSLA-450 Pro Shining3D
Технические параметры 3D-принтера iSLA-450 Pro Shining3D
Параметр | Значение |
---|---|
Размер зоны построения | 450×450×350 мм |
Тип лазера | Nd: YVO4. (500 мВт) |
Скорость сканирования | До 10 м/с |
Точность | 0,1% от линейного размера |
Материалы | Фоточувствительная смола |
Программы | Eplus 3D, Magics |
Скорость построения | До 100 см3/ч |
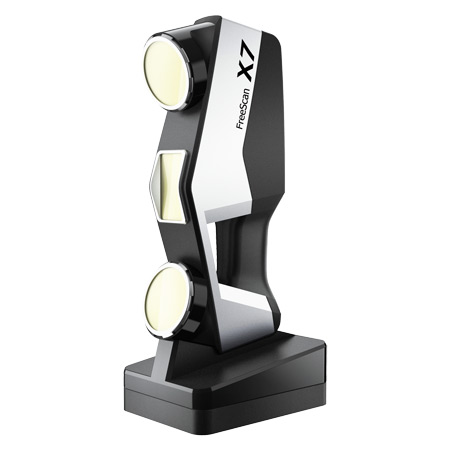
Рис. 22. Портативный 3D-сканер Freescan X7 Shining3D
Технические параметры ручного 3D-сканера FreeScan X7
Параметр | Значение |
---|---|
Точность снимка | 0,03 мм |
Объемная точность (до) | 0,020 мм + 0,025 мм/м |
Скорость сканирования | 480 000 точек/с |
Источник света | 14-лучевой лазерный луч |
Вес | 0,95 кг |
Размер | 130×90×310 мм |