Технология конформных покрытий не нова — она известна несколько десятков лет. Однако, как говорит опыт, этот технологический процесс не всегда принимается во внимание при конструировании. Такое пренебрежение нередко приводит к проблемам на более поздних этапах изготовления новых изделий. Зачастую решение о нанесении конформного покрытия на печатный узел принимается в последний момент, после того как узел провалит испытания на воздействие внешних факторов, а иногда и в ходе эксплуатации. Подобные ошибки несут серьезные потери — и финансовые, и репутационные.
Если не откладывать на потом вопрос о необходимости конформного покрытия, а решить его еще на этапе конструирования, можно избежать целого ряда трудностей при нанесении покрытия и повысить долговременную надежность печатного узла.
Что же нужно учесть при конструировании печатного узла и составлении чертежа конформного покрытия?
Несмонтированная печатная плата
Паяльный резист, нанесенный на несмонтированную печатную плату, может существенно повлиять на нанесение конформного покрытия и долговременную надежность печатного узла.
Для обеспечения хорошей адгезии конформного покрытия и его надлежащего выравнивания без десмачивания и капиллярных эффектов значение поверхностной энергии отвержденного резиста должно превышать 38 дин/см2. На рис. 1 показано, к чему приводит низкая поверхностная энергия при нанесении конформного покрытия.
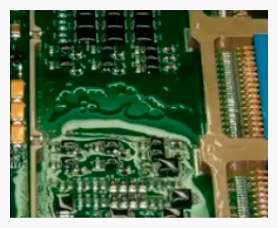
Десмачивание материала
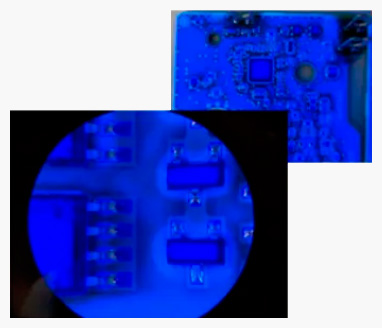
Капиллярные эффекты
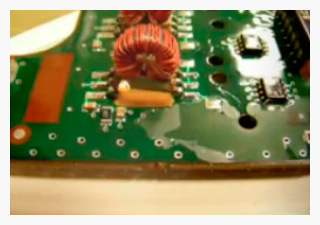
Плохая адгезия
Рис.1. Нежелательные явления, связанные с состоянием поверхности:
- Снижение поверхностной энергии под действием температуры в ходе пайки и загрязнений ведет к плохой адгезии, капиллярным эффектам и десмачиванию.
- Эти явления могут быть также вызваны ненадлежащим выбором паяльного резиста.
- Значение поверхностной энергии печатной платы до нанесения покрытия должно превышать 38 дин/см2.
Во избежание подобных явлений необходимо, чтобы значение поверхностной энергии отвержденного паяльного резиста в технических условиях, предоставленных поставщику печатной платы, составляло не менее 38 дин/см2.
Поверхностная энергия паяльного резиста может снижаться до недопустимых значений под действием температуры в ходе пайки оплавлением, а также из-за остатков припоя.
Поэтому при первоначальной оценке производственного процесса необходимо измерять поверхностную энергию печатной платы по завершении каждой технологической операции, чтобы убедиться, что этот показатель не ниже параметра 38 дин/см2.
Компоновка печатного узла
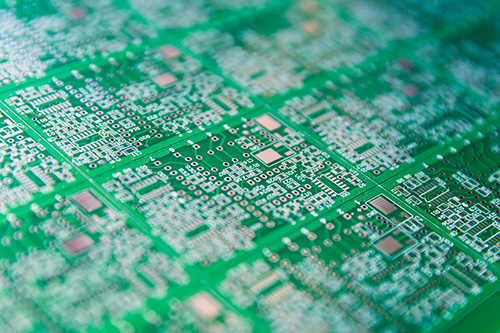
Это следующий шаг, требующий вдумчивого подхода. Нанесение конформного покрытия нередко затрудняется расположением компонентов на плате. Инженеру-конструктору и инженеру-технологу следует обсудить предлагаемую компоновку печатного узла по нанесению конформных покрытий, чтобы оптимизировать компоновку в соответствии с методом нанесения.
В ходе такого обсуждения согласуются и отмечаются на чертеже участки печатной платы, на которых конформное покрытие не требуется.
При этом следует избегать открытых металлизированных сквозных отверстий, так как материал покрытия может стекать по ним и покрывать обратную сторону платы в тех местах, где это нецелесообразно.
Пока не появились флюсы с низким содержанием твердых веществ (в современной терминологии «безотмывочные» флюсы), для обеспечения высокой надежности приходилось выполнять отмывку печатных узлов на последнем этапе производственного процесса, особенно если предполагалось нанесение конформного покрытия.
Эти флюсы выполняли свою задачу во времена аксиальных компонентов, устанавливаемых в сквозные отверстия, с большим шагом между дорожками, да и то при эксплуатации в умеренно жестких условиях. Учитывая сегодняшние технологии с малой толщиной дорожек и высокой плотностью размещения компонентов, а также необходимость обеспечения работы изделия в любых условиях отмывка вновь становится актуальной.
Целесообразность отмывки
Следующее, что предстоит решить перед нанесением конформного покрытия, — это вопрос о целесообразности отмывки.
В зависимости от требуемого уровня надежности и условий эксплуатации остатки флюса могут быть существенным фактором.
В случае нанесения конформного покрытия поверх остатков флюса возникает несколько потенциальных механизмов отказа. Остекловавшиеся остатки флюса могут вызывать растрескивание конформного покрытия и последующий отказ изделия под воздействием жестких термоциклических испытаний, а оставшийся под ними непрореагировавший флюс в условиях высокой влажности может способствовать росту дендритов, что приводит к перемежающимся отказам или полному отказу изделия.
Таким образом, если необходимо обеспечить долговременную надежность печатного узла, рекомендуется его отмывка перед нанесением конформного покрытия.
Существует несколько методов определения уровня чистоты поверхности. Наиболее распространенные: контроль уровня ионных загрязнений и контроль поверхностного сопротивления изоляции.
При контроле уровня ионных загрязнений определяется общее количество ионных солей в мкг/см2 NaCl на поверхности платы после обработки. В 1970-х годах, когда этот метод был только разработан, за норму был принят уровень менее 1,5мкг/см2 NaCl. При сегодняшних технологиях с малой толщиной дорожек и высокой плотностью размещения компонентов следует ориентироваться на уровень ионных загрязнений менее 0,5мкг/см2 NaCl до нанесения конформного покрытия.
Наилучшим методом оценки долговременной надежности является измерение поверхностного сопротивления изоляции. При использовании безотмывочного флюса этот метод покажет, следует ли ожидать неблагоприятных эффектов, вызванных остатками флюса под конформным покрытием.
Если же производственный процесс предполагает отмывку печатного узла, данный метод покажет, все ли загрязнения удалены, в том числе вокруг компонентов и под ними.
Лучше всего выполнять контроль уровня ионных загрязнений и поверхностного сопротивления изоляции на платах-прототипах, чтобы оценить правильность производственного процесса и убедиться в совместимости используемых материалов. Можно осуществлять такой контроль и на этапе массового выпуска, отслеживая отсутствие непредусмотренных изменений в производственном процессе.
Нормативные значения уровня ионных загрязнений и поверхностного сопротивления изоляции следует указать на чертеже конформного покрытия.
Завершая разговор
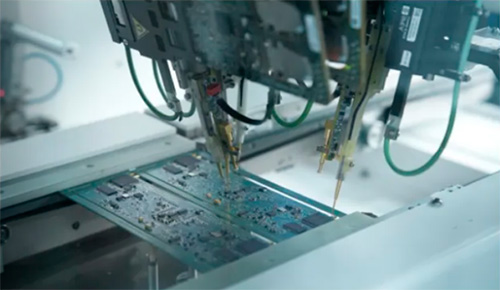
При выборе материала конформного покрытия с учетом условий эксплуатации печатного узла необходимо принимать по внимание следующие факторы:
- диапазон температур, в котором будет эксплуатироваться печатный узел;
- относительная влажность воздуха в процессе эксплуатации;
- наличие конденсированной влаги;
- воздействие опасных веществ и газовых сред;
- минимальный уровень сопротивления изоляции конформного покрытия.
Выбранный материал следует указать на чертеже конформного покрытия.
Для обеспечения долговременной надежности печатного узла важна также правильность нанесения конформного покрытия. В связи с этим необходимо принимать во внимание следующее:
- толщину конформного покрытия;
- необходимость покрытия острых кромок SMT-компонентов;
- исключение возникновения воздушных пузырьков при нанесении;
- исключение десмачивания и капиллярных эффектов на поверхности печатного узла;
- правильную методику отверждения конформного покрытия.
Важно также правильно отвердить конформное покрытие, поскольку несоблюдение параметров отверждения (таких как время, температура, доза ультрафиолетового излучения, если используется УФ-отверждаемое покрытие) ухудшает свойства, а стало быть, и эксплуатационные характеристики готовой пленки конформного покрытия.
Если используемое покрытие содержит УФ-маркер (люминесцентную маркирующую добавку), то визуальный контроль печатных узлов с полностью отвержденным конформным покрытием нужно производить в длинноволновом ультрафиолетовом свете. По свечению маркера можно контролировать полноту покрытия, включая отсутствие десмачивания и капиллярных эффектов, а также осматривать участки, на которых не должно быть конформного покрытия, для уверенности, что покрытие на них не затекло.
Современные автоматизированные системы оптического контроля позволяют также определять толщину конформного покрытия по всей площади поверхности печатного узла, в том числе и непосредственно на технологической линии.
В завершение рекомендуется составить чертеж конформного покрытия печатного узла с указанием перечисленных в статье элементов, а также схему компоновки печатного узла с обозначением участков, на которых конформное покрытие не требуется.
Комментарий специалиста
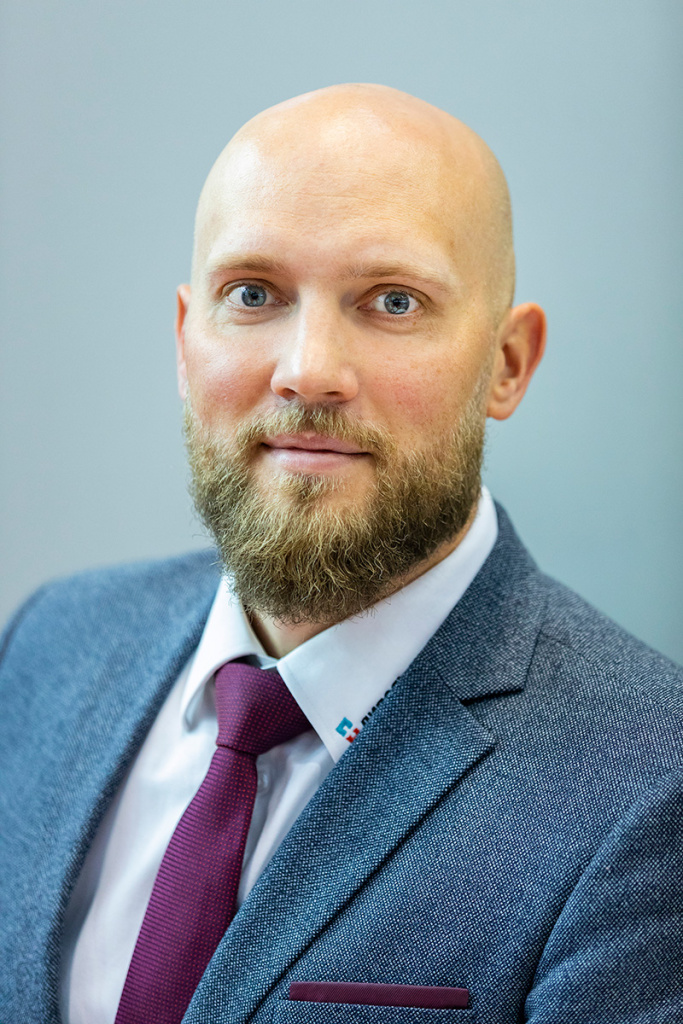
Рис.2. Кирилл Кремлёв, руководитель направления «Оборудование для производства электроники», ГК «Диполь»
Для многих применений в электронике требуется повышенная надежность изделия, которая достигается в том числе и за счет нанесения на изделие конформного покрытия (в российской промышленности часто используется словосочетание «влагозащитное покрытие», но оно не полностью отражает все функции, которые выполняет это покрытие, тогда как в мире распространен термин «конформные покрытия», от слова «конформный» — подобный, повторяющий форму печатного узла). Хочется выразить полную солидарность с мнением, что о нанесении конформного покрытия следует думать заранее, еще на этапе конструирования.
Авторы статьи не акцентируют, что компоновка изделия во многом зависит от способа нанесения конформного покрытия, ограничиваясь фразой о необходимости обсудить этот момент с технологом. Но переводя разговор в практическое русло, есть смысл дать несколько советов конструкторам.
При нанесении лака методом распыления:
- важно учитывать, что для покрытия высоких компонентов необходимо оставлять место для распыляющей насадки, иначе не гарантировано нанесение лака везде, где предусмотрено чертежом;
- если все, что требуется маскировать (защитить от попадания материалов), расположено с краев и в легкодоступных местах, существенно снижаются трудоемкость и количество брака при маскировании/демаскировании.
При селективном нанесении:
- автоматизированная реализация данного метода требует наличия реперных знаков для считывания их установкой. Если лак наносится в несколько слоев, то после нанесения первого контрастность репера существенно снижается. Для таких ситуаций лучше располагать реперы в непокрываемой зоне изделия, например, на технических полях (это могут быть в том числе глобальные реперы на мультиплицированную заготовку);
- если между высокими компонентами находятся зоны, не подлежащие покрытию, то такой участок подлежит маскированию. Поэтому точки для электроконтроля, разъемы, контактные площадки для допайки и т. п. желательно размещать на достаточном расстоянии от высоких компонентов;
- минимизация количества высоких компонентов облегчает процесс селективного нанесения. Также не следует класть высокий компонент набок, если под ним будет наноситься лак;
- сложно ждать селективности с точностью ±1 мм при монтаже высоких DIP-компонентов. Такая невысокая точность особенно характерна для ручной установки. Селективность обеспечивается повторяемостью установки высоких компонентов, иначе лак можно будет распылить только сверху;
- следует избегать DIP-монтажа с зазором. Обеспечить качественное затекание лака под компонент с помощью селективного нанесения (или распыления) будет не просто;
- как и в методе распыления, для покрытия высоких компонентов важно оставлять место для распыляющей насадки, чтобы покрытие могло быть нанесено везде, где необходимо;
- поскольку установки селективного нанесения в основной массе — конвейерного типа (встраиваются в линию), то в случаях, когда требуется покрывать торцы изделия. необходимо использовать дополнительные оснастки. Они позволяют подобраться ближе к краю (торцу) изделия, а также защищают конвейер (цепной или ременной) от попадания материалов.
Окунание:
- если на изделие планируется наносить лак методом окунания, не покрываемые компоненты не следует размещать со всех сторон изделия. Маскирование при использовании метода окунания очень трудоемкий процесс, и его можно избежать, если все, что не требует покрытия на плате, расположить с одной части изделия и оставить эту сторону над поверхностью лака;
- для затекания лака под DIP-компоненты полезно обеспечить тот самый зазор, который был помехой при селективном нанесении;
- перед нанесением лака окунанием плату требуется вымыть. В противном случае значительно увеличивается риск загрязнения и порчи лака.
Основываясь на сказанном выше, можно не только уменьшить количество потенциальных проблем на участке нанесения покрытия, но и существенно снизить затраты на вспомогательные операции, такие как маскирование/демаскирование.