Печатная плата в совокупности с установленными и смонтированными на ней электронными компонентами образует печатный узел. Таким символическим названием этот элемент наделен не зря, ведь от технологии его изготовления зависит как эффективность производства, так и качество конечной продукции.
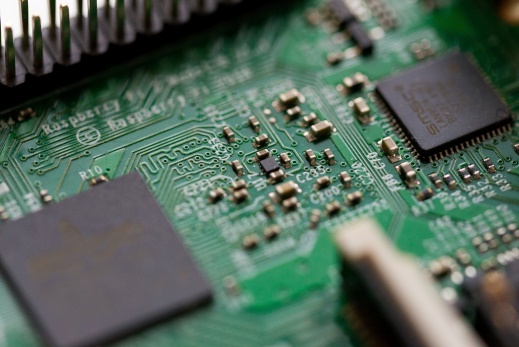
Методы монтажа компонентов на плате
В современной промышленности применяется два способа установки элементов на печатные платы:
- Выводной монтаж (DIP). В это способе выводы электронных компонентов размещаются в сквозных отверстиях, заранее нанесенных на печатные платы, и припаиваются с обратной стороны. Этот метод монтажа появился первым и долгое время оставался основным.
- Поверхностный монтаж (SMD). В этом случае компоненты, оснащенные плоскими выводами, припаиваются непосредственно к поверхности дорожек на плате. За последние 25–30 лет этот метод стал основным. Его основные преимущества: более высокая степень автоматизации и скорость монтажа, возможность использования обеих сторон печатной платы, более компактные размеры элементов и электронного изделия в целом и меньшая себестоимость производства за счет отказа от ручного труда.
Для производства особенно сложных изделий на многослойных платах может использоваться комбинированный монтаж, сочетающий установку выводным и поверхностным методом. При этом практикуются следующие подходы:
- Сначала устанавливаются DIP-компоненты, а затем более мелкие SMD.
- Сначала с помощью средств автоматизации распаиваются SMD, а затем вручную — DIP.
Монтаж всегда осуществляется с помощью припоя, при этом могут использоваться разные его виды.
Типы припоев
Основная классификация припоев достаточно проста. Все припои обычно разделяют на основные классы:
- Мягкие. Имеют температуру плавления до +300 °С и предел прочности 16–100 мПа.
- Твердые. Температура плавления — более +300 °С, предел прочности 100–500 мПа.
Для пайки проводов и электронных компонентов применяются мягкие припои, тогда как твердые обычно используют для пайки медных деталей.
Подобной классификации индустрия придерживалась достаточно долгое время, однако сегодня некоторые специалисты считают, что она морально устарела и не отражает реальной ситуации, поскольку сейчас появились новые виды припоев, которые по назначению и способу применения относятся к мягким, но по характеристикам близки к твердым. По этой причине новая классификация выделяют два вида припоя:
- легкоплавкие — плавятся при нагреве до +400…+450 °С;
- тугоплавкие — свыше +450…+500 °С.
Непосредственно в электронике наиболее универсальным считается оловянно-свинцовый (ПОС), состоящий из смеси олова со свинцом. Его разновидности отличаются соотношением олова и свинца, влияющим на предельную температуру нагрева. К примеру, у ПОС-15 (15% свинца) она составляет +280 °С (ПОС-25 — +260 °С, ПОС-33 — +247 °С, ПОС-40 — +238 °С, ПОС-61 — +183 °С).
Существуют и другие виды припоя для пайки:
- ПОССу (из свинца, олова и сурьмы) — для пайки оцинкованных деталей;
- ПОСК (из свинца, олова и кадмия) — для монтажа элементов, чувствительных к перегреву;
- ПОСВ-50 (с добавлением висмута). Также известен как сплав РОЗЕ. Особенно популярен у новичков-любителей, поскольку имеет низкую температуру плавления — всего +90…+94 °С.
Как известно, свинец при переходе в жидкое состояние выделяет токсичные соединения, поэтому появление бессвинцовых припоев было лишь вопросом времени. Современные технологии используют составы на алюминиевой, цинковой или серебряной основе.
При SMD-монтаже используются паяльные пасты — пастообразные составы, состоящие из флюса, не требующего смывки, олова, свинца и серебра. За счет вязкой консистенции их удобнее наносить на контактные площадки и применять на автоматизированных линиях.
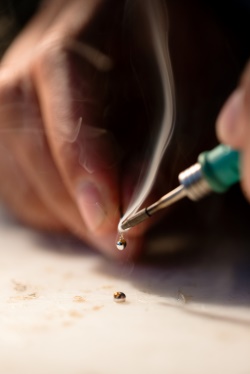
Классификация пайки
Процессы пайки классифицируются по нескольким параметрам. Первая классификация — по синхронизации установки электронных элементов. Он может быть:
- индивидуальной (селективной) — компоненты паяются по очереди или небольшими группами на определенном участке платы;
- групповой — компоненты паяются одновременно за счет общего нагрева.
Далее пайка различается по видам применяемых технологий.
Пайка волной припоя
Метод получил распространение в промышленности еще в середине прошлого века, поэтому оптимизирован под DIP-технологии. Компоненты сначала устанавливаются в монтажные отверстия, места контакта покрываются флюсом, а затем плата помещается над емкостью с расплавленным припоем, поскольку пайка производится с обратной стороны. В емкости создается волна, верхняя часть которой контактирует с выводами контактов.
С распространением SMD-компонентов технология отошла на второй план, в том числе из-за опасности перегрева.
Парофазная пайка (конденсационная)
Активно применяется в производстве электроники, в том числе с SMD-монтажом.
На контактные площадки платы предварительно наносится паяльная паста и размещаются электронные компоненты, после чего плата направляется в конденсационную камеру. В камеру также дополнительно подается жидкость с высокой температурой кипения (до +260 °C), которая при нагреве образует пар и полностью вытесняет кислород, создавая бескислородную среду и обеспечивая идеальное соединение контактов припоем.
За счет относительно небольшого объема камеры подобная технология используется в основном на мелкосерийных производствах. Однако она также предлагает дополнительные преимущества вроде отличной повторяемости и отсутствия перегрева компонентов.
ИК-пайка
Платы пропаиваются в автоматизированной или полуавтоматизированной ИК-печи, которая плавит припой на заданных участках сфокусированными потоками инфракрасного излучения. В печи предусмотрено удаление токсичных испарений, а идеальное качество монтажа обеспечивается предварительным прогревом плат. За счет высокой степени автоматизации, отличной повторяемости и возможности задания индивидуального теплового режима для отдельных зон ИК-пайка оптимальна для промышленного производства плат с высокой плотностью распределения SMD-компонентов.
Конвекционная пайка
Плавка припоя осуществляется за счет потока горячего воздуха. Для предотвращения окисления контактных площадок монтаж также может производиться в бескислородной среде в конвекционной камере или печи.
Стандартная технология состоит из четырех этапов:
- расстановка компонентов на печатной плате;
- предварительный разогрев со стабилизацией температуры;
- плавка припоя;
- охлаждение для фиксации.
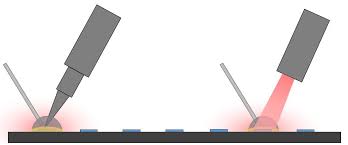
Лазерная пайка
Одна из самых современных и высокоточных технологий. Контакты элементов фиксируются с помощью точечного нагрева мощным лазерным лучом. Лазер автоматизирован и может обрабатывать до 10 точек контакта в секунду. Фактически производительность этой индивидуальной технологии соответствует производительности большинства групповых. Основные преимущества:
- точечная пайка исключает перегрев корпусов компонентов;
- монтаж обеспечивает минимальное окисление контактов, а значит, высокое качество пайки;
- возможность производства печатных плат с крайне высокой плотностью элементов и выводов без дефектов в виде капель припоя или перемычек между контактами.
Ключевой недостаток, существенно замедляющий распространение данного вида пайки — дорогостоящее оборудование.
Заключение
Пайка электронных компонентов — один из ключевых этапов производства электроники. Поэтому при выборе припоя, технологии и оборудования за консультацией правильно обращаться к производителям и поставщикам подобных решений. На сайте группы компаний «Диполь» можно подобрать соответствующие материалы и оборудование для различных технологий пайки: припои, конвекционные печи, системы парофазной пайки, системы селективной пайки.