Ведущий немецкий производитель автомобилей класса «люкс» - компания Porsche начала использовать технологии 3D-печати для изготовления запчастей для своих редких классических автомобилей. Аддитивное производство деталей применяется для техподдержки и восстановления автомобиля, что также выгодно с точки зрения разумного использования ресурсов.
Используя комбинацию технологий 3D-печати (SLM1 для производства металлических деталей и SLS2 для деталей и инструментов из пластика), компания Porsche добавила в свой каталог ряд запасных частей, гарантируя, что автомобили бренда будут и дальше превосходно служить людям.
Для справки:
1Selective Laser Melting - селективная лазерная плавка, метод аддитивного производства, использующий лазеры высокой мощности для создания трехмерных физических объектов за счет плавки металлических порошков.
2Selective Laser Sintering - метод аддитивного производства, используемый для создания функциональных прототипов и мелких партий готовых изделий, основан на последовательном спекании слоев порошкового материала с помощью лазеров высокой мощности.
Экономичное решение для замены стандартных деталей
Поскольку автомобили Porsche Classic пользуются большим спросом в качестве предметов коллекционирования, их серия имела небольшой производственный цикл с малыми партиями. Изготовление и хранение большого числа оригинальных запасных частей для этих автомобилей, учитывая их низкий количественный спрос, не имела под собой финансового смысла. Это в свою очередь, создало ряд трудностей, когда запчасти необходимы для моделей, ставших автомобильной классикой.

Крышка топливного бака, выполненная с использованием технологии 3D-печати
В настоящее время ассортимент для Porsche Classic включает около 52 000 наименований деталей. Когда какая-то запасная часть оригинальной серии выходит из строя, для ее воспроизведения требуется специальная оснастка. Создание специальных инструментов, также как и самих деталей, целесообразно для больших партий, в то время как небольшие партии, могут быть не оправданы.
Успешное проведение испытаний и расширение перечня доступных запчастей
Обратившись к 3D-технологиям, компания Porsche выбрала инновационный подход к созданию запасных частей для снятых с производства автомобилей Porsche 959. 959-я модель выпускалась компанией Porsche с 1985 по 1988 годы малыми партиями и была одним из лучших спортивных автомобилей того времени. В настоящее время такой автомобиль представляет весьма редкий и желанный для коллекционеров экземпляр.
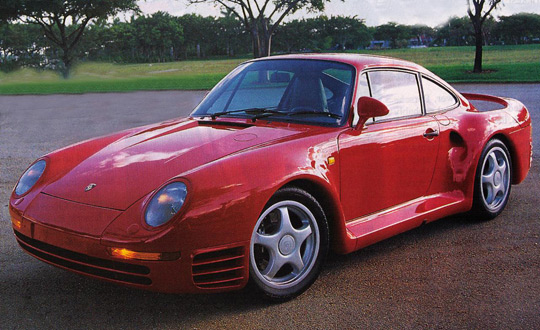
Коллекционная модель Porsche 959
Изготовленный по технологии SLM рычаг сцепления, после проведения испытаний, продемонстрировал полное соответствие требованиям, предъявляемых для оригинального компонента. С тех пор компания добавила еще восемь пластмассовых деталей в свою библиотеку оцифрованных запасных частей, включая крышку бензобака, рычаг кривошипа и часть тормоза.
Изготовленные по пресс формам пластмассовые детали, полученные методом SLS, подвергаются очень жестким испытаниям. Например, некоторые их них должны иметь устойчивость к маслам, топливу, кислотам и свету.
В качестве пилотного проекта на ближайшее будущее, компания запланировала модернизировать еще двадцать запасных частей. Но и это еще не предел, так как технология 3D-печати имеет достаточный потенциал для охвата гораздо большей части продукции компании Porsche.
3D-печать как наиболее экономичное решение
Производители автомобилей все чаще прибегают к 3D-печати, используя ее для изготовления деталей и инструмента. И в этом нет ничего сверхъестественного. Так, например, компания Volkswagen ежегодно экономит 160 000$ за счет 3D-печати компонентов для своей заводской сборочной линии на предприятии Autoeuropa в Португалии.
Аналогичным образом, поступила и компания Mercedes-Benz Trucks, которая запускает проект под названием Digital Spare-Part Initiative (инициатива по созданию запасных частей посредством цифровых технологии), по производству компонентов для своих автомобилей. Напечатанные на 3D-принтере детали, по сравнению с их литыми аналогами, имеют 100% плотность и лучшие показатели чистоты металла.
Такого же подхода придерживается и компания-партнёр, с которой у Mercedes-Benz Trucks имеются тесные дружественные связи, Daimler Trucks, которая уже достаточно давно использует запасные части полученные методом 3D-печати по технологии SLS.
Еще один известный производитель – компания Ford, на своей сборочной линии использует 3D-печать непосредственно на месте сборки и выпуска SUV3 нового поколения. В результате чего, время, затраченное на замену сломанного инструмента или деталей для Ford Escape и Lincoln MKC, сокращается с нескольких недель буквально до нескольких часов.
Для справки:
3Sport Utility Vehicle - спортивно-утилитарный автомобиль, североамериканский тип автомобиля, официально классифицируемый как лёгкий грузовик (light truck), но при этом предназначенный для повседневной эксплуатации в качестве пассажирского транспорта.
Вместе с новыми компьютерными вычислительными и аналитическими системами в общей системе управления предприятием, которые использует компания Ford на своем заводе в Луисвилле, штат Кентукки, работники завода теперь могут загружать проекты запасных частей и создавать инструменты для конкретных операций, переходя от концепции к готовому объекту за два часа. 3D-печать также значительно сократила на 250 000$ затраты, которые компания Ford тратила для изготовления прототипа.
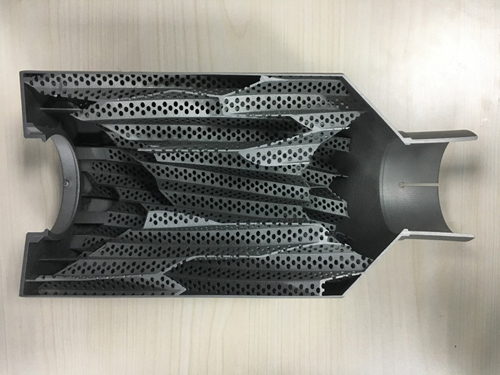
Автомобильная деталь изготовленная на промышленном 3D-принтере Shining 3D
Технологические решения от «Диполь»
На условиях эксклюзивного партнерства, компания «Диполь» поставляет промышленные 3D-принтеры производства Shining 3D, работающие по технологиям SLM и SLS. Выбрать подходящее технологическое решение, а также ознакомиться с моделями и купить промышленный 3D-принтер для литейного производства или стереолитографии можно на нашем сайте или обратившись к менеджерам.