В нашем журнале «Эксперт+» мы регулярно рассказываем о заказчиках, являющихся стратегическими партнерами компании «Диполь». Не так давно их ряды пополнила калужская компания «Автоэлектроника». Предприятие развивается и оптимистично смотрит в будущее, постепенно расширяя ассортимент изделий, наращивая производственные мощности и используя передовое оборудование.
Справка
АО «Автоэлектроника» специализируется на разработке и изготовлении электронных автокомпонентов и систем для крупнейших производителей автомобилей России и ближнего зарубежья. Компания динамично развивается, получая награды за достижения в разных областях деятельности как от своих партнеров, так и от представителей власти. «Автоэлектроника» входит в состав предприятий — членов союза «Торгово-промышленная палата Калужской области», является одним из учредителей ассоциации «Кластер автомобилестроения и автокомпонентов Калужской области» и членом ассоциации предприятий машиностроения «Кластер автомобильной промышленности Самарской области».
Калужский завод электронных изделий (АО «Автоэлектроника») создан в 1990 году на базе конструкторского бюро электроники и цеха № 8 Калужского завода автомотоэлектрооборудования (КЗАМЭ). Первыми подразделениями компании были цеха по производству реле регуляторов и блоков экономайзеров, систем управления климатом, цех микроэлектроники и собственное конструкторское бюро.
В настоящее время предприятие оснащено оборудованием по сборке и контролю изделий с использованием поверхностного монтажа, имеет производственные мощности по изготовлению печатных плат, а также изделий по толстопленочной гибридной и полупроводниковой технологии с использованием автоматизированного проектирования.
Собственная испытательная база, оборудованная климатическими камерами и камерами влажности и соляного тумана, позволяет проводить все виды испытаний изделий.
С 1998 года на предприятии внедрена и сертифицирована система менеджмента качества по версии международного стандарта ISO. На сегодняшний день СМК соответствует требованиям IATF 16949-2016 и ISO 9001-2015.
Основные виды выпускаемой продукции:
- электромеханические усилители руля (ЭУР);
- цифровые тахографы;
- датчики ЭСУД (давления, скорости, фаз и др.);
- системы отопления салона;
- электрооборудование пусковых, подогревательных, отопительных устройств;
- элементы управления (модули управления светотехникой, регуляторы освещения приборов, переключатели корректора света фар, цифровые часы);
- регуляторы напряжения и реле.
ЭУРУ — до и после сборки
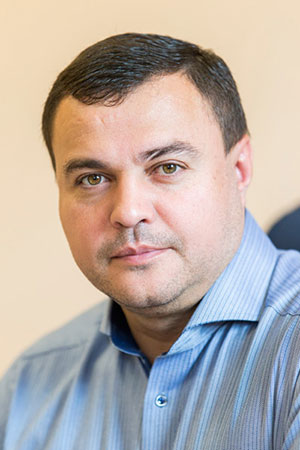
Генеральный директор АО «Автоэлектроника» Руслан Дурдыбаев
Потребителями продукции АО «Автоэлектроника» являются практически все автомобильные заводы России и СНГ, основные из них — ПАО «АВТОВАЗ», АО «Автомобильный завод «ГАЗ», ПАО «КАМАЗ».
Я веду беседу с Русланом Дурдыбаевым, генеральным директором АО «Автоэлектроника».
— Руслан Рустамович, представьте, пожалуйста, вашу компанию и главные направления ее деятельности.
— Мы производим электронные компоненты собственной разработки для автомобильной промышленности. Основа нашего развития — освоение продукции для современных моделей российских заводов и сотрудничество с иностранными предприятиями, которым интересен бизнес в России. Основные автомобильные заводы России — это АВТОВАЗ и КАМАЗ, и для каждого у нас есть своя линейка продуктов.
Наиболее значимым изделием в доле поставок на ПАО «АВТОВАЗ» является электромеханический усилитель рулевого управления (ЭУРУ). Мы начали поставлять его с 2006 года и с тех пор постоянно совершенствуем продукт и участвуем в проектах развития ПАО «АВТОВАЗ». Последние модели АВТОВАЗа — VESTA и X-RAY. Электроусилители для этих автомобилей представляют новый для нас уровень разработки с точки зрения технических характеристик, который полностью соответствует европейским автомобильным стандартам, включая стандарт функциональной безопасности ISO 26262. Благодаря слаженной работе команды мы смогли закончить проект и начать поставки усилителя на модель X-RAY CROSS в 2018 году, а в 2020-м начнем поставлять ЭУРУ на модельный ряд VESTA.
Процедура обкатки — функциональный контроль готовых изделий
Для второго автомобильного гиганта России — КАМАЗа — у нас есть проект «Тахограф». Изделие серийно выпускается c 2015 года и содержит программно-аппаратное шифровальное (криптографическое) средство (СКЗИ). Тахограф ТЦА-02 НК разработан по требованиям Европейских нормативно-технических документов (ЕСТР) и включен в перечень о моделях тахографов, разрешенных к установке на транспортные средства, эксплуатируемые на территории РФ. В настоящий момент тахографы АО «Автоэлектроника» поставляются на конвейеры крупнейших российских автозаводов.
Еще одно приоритетное направление — развитие контрактного производства. В 2015 году нами заключено соглашение с компанией Clarion Japan и Hitachi Rus. По планам мы должны были собирать телематический модуль ЭРА-ГЛОНАСС (TCU) с последующей реализацией его в компании Ford Sollers. Мы успешно провели первый этап по общей сборке, и в 2019 году должен был начаться второй этап сотрудничества — сборка полного цикла, для которой закуплено новое автоматизированное оборудование. К сожалению, в связи с уходом производства Ford с территории РФ, нам придется искать других партнеров для изготовления продукции на заказ. Впрочем, это вполне выполнимо, поскольку «Автоэлектроника» уже имеет опыт выпуска высокотехнологичных изделий и сотрудничества с мировыми производителями, с одной стороны, а с другой — локализация является необходимым условием плана мероприятий по импортозамещению в отечественной автомобильной промышленности в соответствии со стратегией Минпромторга России. Мы уже серьезно проинвестировали этот проект за счет покупки современного оборудования. Установленная технологическая линия позволяет работать в режиме производства полного цикла, начиная от монтажа печатной платы и заканчивая получением готового изделия. Спектр выполнения операций: нанесение паяльной пасты, контроль паяльной пасты, монтаж радиокомпонентов, оплавление, автоматический и оптический контроль, рентген-контроль, селективная пайка, мойка. Уверены, что у нас есть достаточный опыт и рейтинг предприятия на индустриальной арене автопроизводителей в РФ, чтобы обеспечить себе новые контракты.
Полностью автоматическая гибкая высокоточная линия поверхностного монтажа
— С чем вы связываете уход такого крупного заказчика, как Ford?
— Думаю, это последствия внешнеполитических баталий, санкционного давления и положения бизнеса марки на рынке не только России, но и Европы. Как показала практика, концепция продаж одинаковых автомобилей One Ford на совершенно разных рынках неэффективна и единого решения для всех не существует.
Уход Ford из России хоть и является для нас поводом для беспокойства, но и не такое переживали. Это серьезный индикатор того, что бизнес может не поспевать за рынком. В современных реалиях нужны новые гибкие механизмы управления и готовность к изменениям.
Нашей компании уже почти 30 лет, и мы прошли не один кризис. Мы понимаем, что любой кризис — это не только проблема, но и возможность. Возможность что-то разработать, пересмотреть подход, овладеть новыми навыками, то есть все то, что позволит выйти из сложной ситуации с новыми приобретениями. Именно такая философия позволяет развиваться и стабильно увеличивать объем продаж.
— А как вы можете охарактеризовать ваш рынок в целом? Не чувствуете «провисания»?
— Если мы говорим о рынке автокомпонентов в целом, то, конечно, с учетом снижения объема производства автомобилей в России спад неизбежен. Но, предполагая нестабильную ситуацию на рынке, мы вкладывали силы и средства в новые продукты, расширение ассортимента. И в итоге, даже с учетом ухода Ford, нам удается удерживать стабильные объемы. Сейчас идем даже с небольшим ростом — около 12–13 процентов (с Ford были бы все 30).
Например, в этом году мы рассматриваем варианты сотрудничества с компанией Volvo в рамках государственной программы локализации производств. Работа ведется по двум нашим продуктам — тахограф и ЭРА-ГЛОНАСС. А еще по одному основному продукту — электроусилитель рулевого управления —по результатам мониторинга рынка нас нашли иранские автопроизводители. А иранский рынок, между прочим, это 1,5 млн автомобилей.
Мы понимаем, что рассчитывать на увеличение объемов производства можно, если привлечь на наши площади крупных локальных и мировых игроков. В рамках расширения объемов контрактного производства идут переговоры с Valeo, Hitachi, NSK, JTEKT. С некоторыми уже подписаны меморандумы о сотрудничестве, с другими пока определяются направления нашего сотрудничества.
Если говорить о конкурентной среде в части основных наших изделий, то, с одной стороны, есть конкуренция, которая не позволяет расслабиться, с другой — конкурентов не так много и они известны. Есть мировые бренды, есть отечественные производители, и, следя за новинками друг друга, мы выводим свои продукты на новый уровень.
Иная ситуация в сегменте aftermarket. Наибольшую проблему для нас, и наверняка для других производителей тоже, представляют подделки китайских умельцев. Да, это неудобство, но не критичное, хотя и оттягивает силы на ведение разбирательств по поводу контрафакта и контрабанды и на продумывание новых методов защиты нашей продукции.
Мы готовы развиваться и искать новые решения в условиях конкуренции. Остается надеяться, что не будет каких-то глобальных внешнеполитических потрясений.
Сущность процесса локализации заключается в стремлении зарубежных компаний обеспечить свои сборочные производства на территории России комплектующими российских производителей. Увеличение числа иностранных сборочных производств и глубины локализации способствует росту объемов заказов отечественным производителям, что в свою очередь обеспечивает как развитие производств территории, так и возможность преодоления зависимости экономики региона от импортных поставок.
— Вы работаете в отрасли, где к продукции предъявляются особые требования по надежности. Как у вас решен вопрос с контролем качества и прохождением испытаний?
— Испытательная лаборатория в АО «Автоэлектроника» отвечает всем необходимым условиям выполнения измерений в закрепленной за ней области деятельности. Оснащение лаборатории позволяет проводить такие исследования, как:
- проверка внешнего вида, массы;
- испытания на теплостойкость и теплоустойчивость;
- испытания на холодостойкость;
- испытания на циклическое воздействие температур;
- испытания на влагостойкость;
- испытания на воздействие соляного тумана;
- проверка механической прочности выводов;
- испытания на вибро-ударопрочность;
- испытания на наработку.
Также мы проводим эксперименты, используя в качестве испытательной базы автопарк предприятия. Ставим на них свои усилители, реле, датчики. Это позволяет нам, не дожидаясь отзывов заказчика, наглядно увидеть, какие могут быть риски, проблемы. И оперативно внести исправления.
Ну и конечно, много внимания уделяется качеству на этапе сборки печатных плат. Мы используем автоматические измерительные 3D-системы Kohyoung для контроля качества нанесения паяльной пасты и контроля печатного узла, а для проверки качества производственных процессов на участке инспекции предусмотрена система рентгеновского контроля Quadra 5.
Kohyoung Zenith Lite — автоматическая измерительная 3D-система для обнаружения дефектов, сбора данных и статистического анализа
Новейшая высокоэффективная система рентгеновского контроля Quadra 5 (производитель Nordson Dage) для проверки собранных изделий на скрытые дефекты
— Руслан Рустамович, ваше предприятие одно из самых крупных в Калужской области, известной сосредоточением высокотехнологических производств. Есть ли у вас проблема кадрового голода и как вы ее решаете?
— Дефицит квалифицированного персонала, как среди рабочих, так и среди инженеров — насущная проблема. Мы делаем ставку на активную кадровую политику, направленную на повышение уровня квалификации персонала, совершенствование системы мотивации и профессионального развития. Особое внимание уделяется обеспечению социальной защищенности сотрудников. В 2019 году, например, мы стали победителями IV региональной HR-премии «Работодатель года — 2018» в отрасли приборостроения и электроники.
В июне 2019 года предприятие участвовало в национальном проекте «Повышение производительности труда и поддержка занятости», который предусматривает реализацию мероприятий по повышению производительности труда и оптимизации бизнес-процессов.
Также мы принимаем участие в программе по переподготовке сотрудников предпенсионного возраста — направляем их на повышение квалификации и обучение новым специальностям. Это очень важная поддержка на уровне государства, потому что специфика автопрома требует постоянного обновления технических требований, усовершенствования знаний и навыков, и мы просто обязаны держать руку на пульсе.
Работа с молодыми специалистами является одним из приоритетных направлений кадровой политики. «Автоэлектроника» тесно сотрудничает с учебными заведениями высшего и среднего профессионального образования: КФ МГТУ им. Н. Э. Баумана, Калужским техникумом электронных приборов, Калужским транспортно-технологическим техникумом им. А. Т. Карпова, Калужским техническим колледжем. Студенты проходят практику на наших производственных площадях и начинают свой трудовой путь уже в период обучения.
В наших планах и создание так называемой Фабрики процессов. Мы позаимствовали эту идею у коллег и хотим распространить ее у себя. Суть Фабрики в том, что любой человек, даже без опыта работы, может поучаствовать в производственном процессе и после этого поделиться своими впечатлениями, предложениями по оптимизации.
Рабочее место на участке подготовки производства
Автоматизированная система отмывки трафаретов N29Auto (производитель MBTech)
Интеллектуальные автоматизированные системы хранения SMD Tower (производитель Mycronic)
Интеллектуальные автоматизированные системы хранения SMD Tower (производитель Mycronic)
— Какие еще цели стоят перед предприятием?
— Основная задача — непрерывное развитие. Эта сжатая формулировка подразумевает очень многое. Разработки новых проектов и борьба за стабильность производственного процесса. Налаживание взаимоотношений с иностранными автосборочными предприятиями и крупными локальными производителями. Работа с создающимися сейчас едиными центрами разработок. Рост благосостояния сотрудников. Поиск новых решений и нестандартных подходов.
Хочу подчеркнуть: электронная (интеллектуальная) компонента в современном автомобиле все больше увеличивается и составляет значительную часть его стоимости. Так что пути для развития, безусловно, есть.
Комментарий специалиста
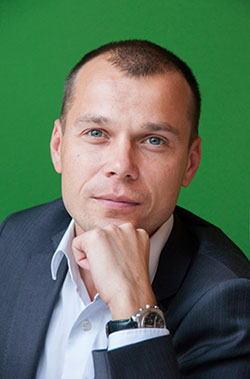
Дмитрий Иванов, коммерческий директор АО «Диполь Технологии»
Данный проект начал свое развитие с выставки «Экспоэлектроника» в 2016 году. Тогда на стенде «Диполя» мы встретились со специалистами компании «Автоэлектроника» и узнали о стоящих перед ними задачах по расширению производственных мощностей. Сразу после окончания выставки была создана рабочая группа, и началась всесторонняя проработка проекта. Надо отметить, что задачу нам предстояло реализовать масштабную и отнюдь не тривиальную. Было необходимо разработать проект комплексного технического перевооружения крупного предприятия под выпуск новых изделий, и при этом наше предложение должно было оказаться лучше решений многочисленных компаний-конкурентов. Следовало учесть и то, что конечным заказчиком изделия выступала японская компания Clarion — требования к подбору технологий, оборудования, оснастки предъявлялись самые жесткие.
В том же году заказчик сделал выбор в пользу нашей компании, предложившей оптимальное решение, максимально соответствующее поставленным задачам. Практически весь следующий год ушел на различные согласования, был подписан контракт, и началась основная фаза реализации проекта.
Возвращаясь к задачам, хотелось бы отметить, что основными из них были высокая скорость, достаточная для сборки массового продукта, высокая точность, максимальная гибкость, контроль на каждом этапе и полная прослеживаемость вплоть до уровня каждого установленного компонента. Если весь технологический цикл сборки нового изделия разбить на этапы, то компанией «Диполь» были оснащены под ключ следующие из них:
- Линия поверхностного монтажа на базе пары установщиков Mycronic серии DX, которые отличает «скорострельность» в совокупности с высокой точностью и максимальной гибкостью, позволяющей осуществить переналадку на следующее изделие за минуты. Данная линия также оснащена двумя автоматическими измерительными 3D-системами Koh Young для контроля качества нанесения паяльной пасты и контроля печатного узла после процесса пайки, высокоэффективной девятизонной конвекционной печью Heller. Линия контролируется с помощью интеллектуального программного комплекса, который управляет всеми этапами: подготовка производства, переналадка, прослеживаемость, аналитика.
- Участок отмывки трафаретов представлен полностью автоматической отмывочной машиной MBTech N29Auto, работающей по замкнутому циклу.
- Участок штыревого монтажа оснащен высокоскоростной модульной системой селективной пайки Synchrodex от компании Pillarhouse. Помимо высокого качества пайки, преимущество данной системы определяется ее конструкцией. Фактически установка может расти вместе с увеличивающимися объемами производства путем добавления дополнительных модулей.
- Участок инспекции оснащен системой рентгеновского контроля Quadra 5 от компании Nordson DAGE. Данная система показывает лучшее в своем классе качество изображения за счет точного распознавания всех компонентов и деталей рисунка размером до 100 нм.
- Участок хранения комплектации оснащен пятью полностью автоматическими системами хранения Mycronic SMD Tower 8000. Общее количество хранимых в защищенной атмосфере катушек с SMD-компонентами — 5740 штук. Необходимо отметить, что такие системы хранения работают в единой информационной среде с линией поверхностного монтажа, осуществляя выдачу нужного компонента при его окончании на линии, получая информацию о количестве израсходованных компонентов.
Все участки оснащены промышленной мебелью VIKING, производимой компанией «Диполь» и занимающей лидирующие позиции на российском рынке.
Материал подготовил Алексей Смышляев, главный редактор журнала «Эксперт +», компания «Диполь»
Фото: Алексей Смышляев