Денис Бычковский, к. ф.-м. н., генеральный директор ООО «Аддитивные технологии»
Александр Неткачев, технический директор ООО «Аддитивные технологии»
Отечественное литейное производство является основной базой машиностроительного комплекса. Перспективы литейной отрасли определяются темпами развития машиностроения, потребностью в литых заготовках, динамикой их выпуска, уровнем развития литейных технологий и конкурентоспособностью отечественных предприятий
По данным последних лет, в России действует около 1250 предприятий, изготавливающих отливки, оборудование и сопутствующие материалы. Однако уровень автоматизации литейного производства в нашей стране крайне низок — 78% отливок выпускаются на механизированных линиях и машинах, а также вручную. В связи с этим разработка автоматизированных методов создания литейных форм становится одним из приоритетных направлений развития отрасли.
Проблема и решение
В транспортном машиностроении сегодня широко используются высокотехнологичные двигатели внутреннего сгорания. В их конструкцию входят сложные по форме и зачастую крупногабаритные блоки цилиндров и головки блоков цилиндров, которые изготавливаются российскими предприятиями по традиционным технологиям литья. Первая из них — литье в одноразовые формы, сделанные вручную с помощью физических мастер-моделей. Для этого требуется длинная технологическая цепочка изготовления мастер-модели, подготовки смеси, формовка и сушка частей формы, места для хранения моделей и так далее. Другая технология — литье в кокиль (металлическую форму) — очень затратна по времени (от 6 месяцев до 1–2 лет), трудоемка и экономически невыгодна, а кроме того, данный способ сопряжен с высоким риском брака при изготовлении кокиля. Оба подхода имеют технологические ограничения на сложность внутренней конфигурации отливки. Применяя перечисленные технологии, невозможно или крайне затруднительно выполнить сложные каналы охлаждения, оптимизировать конструкцию и снизить припуск на последующую обработку. Все это значительно ограничивает потенциал разработки новой продукции и осложняет выпуск новых моделей, увеличивает сроки выхода новинок на рынок и стоимость запуска в производство, что, в свою очередь, негативно сказывается на конкурентоспособности конечной продукции. Проблемы с невозможностью реализации наилучших расчетных конфигураций конструкции традиционными методами ведут к снижению эксплуатационных характеристик продукции.
В последнее время для преодоления технологических ограничений и ускорения сроков проектирования и производства мировые лидеры машиностроения активно внедряют аддитивные технологии. Создание литейных форм методами послойного синтеза позволяет обойти технологические ограничения традиционных способов и сократить производственную цепочку, отказавшись от таких операций, как изготовление мастер-модели из металла или композитных материалов, изготовление литниковой системы и прибылей, формовка частей формы (установка мастер-модели и литниковой системы в опоку и засыпка смесью). Это приводит к сокращению времени производства и снижению на порядок стоимости формы.
Для примера рассмотрим изготовление литейного стержня для формирования внутренних каналов охлаждения двигателя различными методами (рис. 1). Как видно из приведенного примера, стоимость изготовления формы с использованием разрабатываемой технологии на три порядка меньше, чем по любой другой технологии. Подобный экономический эффект достигается за счет того, что 3D-принтер создает литейную форму сразу по цифровой модели. Такая модель разбивается на слои и передается в 3D-принтер, в котором отвердитель наносится согласно цифровой модели литейной формы на предварительно подготовленный слой песчаной смеси. В результате в зоне построения создается отвержденная часть песчаной смеси, точно повторяющая цифровую модель.
Изделие | Объем стержня | Материал | Линейные размеры стержня |
---|---|---|---|
Литейный стержень для формирования внутренних каналов охлаждения двигателя | 300 см3 | удаляемый из отливки песок (гипс) | 300×216×85 мм |
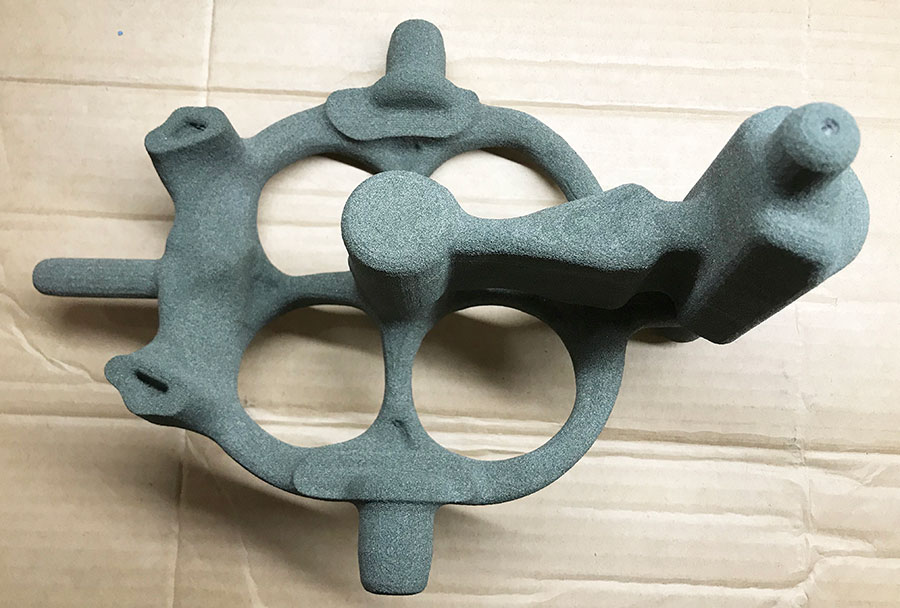
Рис. 1. Сравнение методов изготовления литейного стержня
Технология | SLA и SLS 3D-печать | Станок с ЧПУ | Песчано-полимерная 3D-печать |
---|---|---|---|
Стоимость, руб. | 46560 | 21560 | 45 |
Время, дней | 9 | 24 | 1 |

Рис. 2. Напечатанная форма для отливки блока головки цилиндров в сборе с литейными стержнями
Технологии печати, применяемые для производства литейных форм
Для производства литейных форм методом послойной печати предназначены технологии струйной печати и спекания плакированного песка.
Технология струйной печати была разработана в Массачусетском технологическом институте (MIT, US) в начале 1990-х годов и носит название Binder Jetting (BJ) (ее принцип описан в пионерских патентах MIT под названием «3D printing techniques» US5204055 от 20.04.1993, US5340656 от 23.08.1993, US5387380 от 07.02.1995). Технология BJ представляет процесс послойного синтеза, в котором жидкий связующий агент избирательно осаждается для соединения частиц порошка. Печатающая головка наносит связующий материал на слой порошка в соответствующих участках. Рабочая камера опускается, и затем наносится следующий слой порошка, в который вновь добавляется связующий состав. Технология позволяет печатать крупные детали и зачастую более рентабельна других методов производства.
В технологии BJ применяют силикатный песок (преимущественно с фурановым связующим). Силикатный песок, получаемый из кристаллов кварца, — один из наиболее распространенных сортов песка, он широко используется, в том числе для создания пресс-форм и сердечников для промышленных отливок. Фурановое связующее не требует обжига является типичной традиционной основой в песчаных отливках, и его применение не требует внесения изменений в литейный процесс. Причем напечатанные формы сразу доступны для литья.
Также для печати могут использоваться керамические порошки, состоящие из силиката алюминия и обладающие отличными огнеупорными свойствами, высокой проницаемостью и низким тепловым расширением. Газы в них легко диспергируются, уменьшая потенциальную пористость при литье (создание таких газопроницаемых форм, в том числе с применением керамики, описано в патенте EP1773559 от 18.04.2007 «Gas permeable molds»). Формы, отпечатанные из таких керамических порошков, особенно рекомендуются для литья стальных сплавов или печатных сердечников, подверженных высоким термическим напряжениям.
К недостаткам известного решения следует отнести необходимость применения большого количества связующего вещества и активатора для получения достаточной прочности формы. Это ведет к большему выделению вредных веществ в рабочую зону при построении формы и при заливке металла, увеличивает газовыделение, что в свою очередь вызывает появление дефектов в отливке и увеличивает стоимость изготовления.
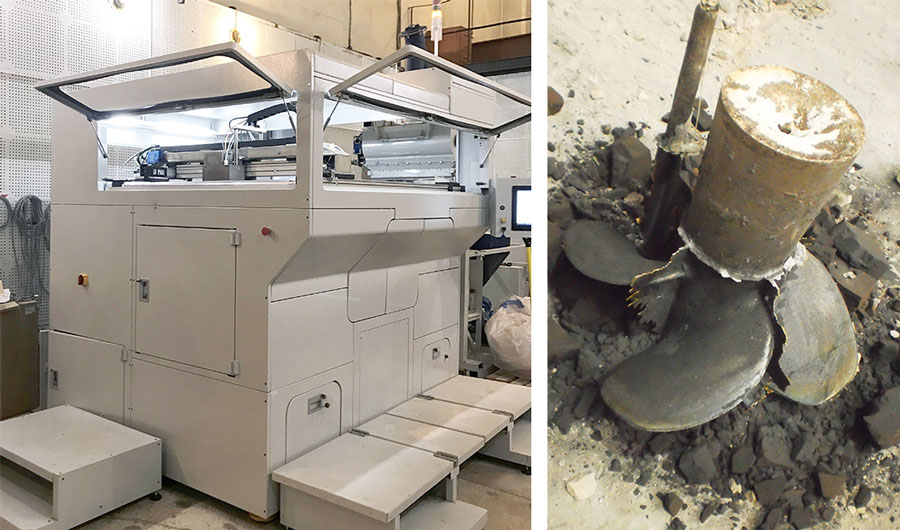
Рис. 3. Литейная форма для отливки гребного винта корабля и полученная отливка
Следует сравнить технологию струйной печати при производстве литейных форм с технологией лазерного спекания плакированного песка. В данном случае печать осуществляется за счет спекания песчинок, покрытых тонкой оболочкой смолы. Как и в случае струйной печати, песок наносится последовательно слоями, а каждый слой обрабатывается лазерным лучом. Главными параметрами для сравнения служат скорость построения и себестоимость получаемых форм. По скорости построения лазерные машины сильно уступают струйным. При одинаковых размерах зон построения скорость печати лазером в 10 раз ниже, чем струйной при толщине слоя, близкой к 200 мкм, что находится на грани возможностей технологии. Если толщина слоя находится в пределах 100 мкм, то скорость печати уменьшится еще больше и будет отставать от струйной печати почти в 20 раз. Таким образом, строить большие формы, размеры которых близки к 1 м или более, по этой технологии просто невозможно. Сравним теперь себестоимость формы, отбросив для простоты расчетов отчисления на амортизацию, стоимость рабочего времени и сопоставляя только стоимость песка. При струйной печати требования, предъявляемые к песку для печати, практически такие же, как и при классическом процессе с холодно-твердеющими смесями (ХТС). На практике это означает, что физико-химические свойства песка такие же, как при классическом процессе с ХТС. Однако для песка, используемого в принтерах, существуют более жесткие нормативы однородности. Если при ручной формовке размеры песчинок и их форма не имеют значения, то при работе с принтером необходим максимально однородный песок. Это требование критично для равномерного нанесения микроскопических слоев. Речь идет о толщинах, находящихся в пределах 200–500 мкм. Очевидно, что при такой величине размер песчинок становится соизмеримым с толщиной слоя и следует использовать однородный песок для лучшего распределения частиц по всему объему. Данное условие несколько удорожает песок, применяемый в 3D-печати, по сравнению с используемым при ручной формовке, но средняя стоимость за 1 тонну не превосходит 5 тыс. рублей. Стоимость же плакированного песка колеблется в пределах 170–340 тыс. рублей за 1 тонну, в зависимости от его марки. Таким образом, если сравнить стоимость плакированного и литейного песка для 3D-печати, то окажется, что плакированный песок дороже в 30–60 раз! Такая «космическая» стоимость делает производство литейных форм абсолютно неконкурентоспособным. Кроме того, в России подобный песок не производится, что накладывает дополнительные риски, связанные с регулярностью поставок, даже если бы эта технология стала применяться.
Отечественные 3D-принтеры для литейных производств
Установки с большой рабочей зоной для одновременной печати нескольких однотипных форм позволяют применять технологию песчано-полимерной печати для выпуска серийных и крупносерийных партий деталей. Кроме того, использование данной технологии реализует переход к цифровому производству.
Зарубежные технологии для создания песчано-полимерных литейных форм развиваются с 80-х годов XX века. Основными игроками в этой сфере являются компании ExOne и Voxeljet. Несмотря на ряд достоинств, машины этих фирм обладают и некоторыми недостатками, затрудняющими их проникновение на рынок:
- Высокое газовыделение при заливке металла с высокой температурой плавления в песчаные формы, что ограничивает использование установок при литье жаропрочных сталей и сплавов.
- Стоимость оборудования, которая в зависимости от размера камер может колебаться от одного до нескольких миллионов евро.
- Стоимость расходного материала и зависимость от его поставок. Отечественные материалы не могут заместить импортные в силу особенностей технологии, используемой в импортных установках.
Естественно, на фоне этих обстоятельств отечественные разработчики должны были задаться созданием принтера, способного конкурировать с западными аналогами. Так, в 2016 году наша компания ООО «Аддитивные технологии» разработала собственную технологию послойной печати, на которую были поданы две патентные заявки и получен приоритет. Через год уже был собран первый отечественный песчано-полимерный принтер АТ300. Он имел камеру построения 500×300×300 мм (X, Y, Z) и обеспечивал рост слоя толщиной 3,2 см/ч, что соответствовало скорости построения 4800 см3/ч, или 45 с на один слой по вертикали (координата Z). Скорость, прямо скажем, не высокая, но для первой модификации вполне подходящая. Запуск первой модели АТ300 позволил отточить все аспекты технологии, а также отработать систему управления печатью.
Система состоит из двух основных блоков: управление приводами и управление непосредственно печатью (движение головок, впрыск связующего). Усовершенствования системы, достигнутые в результате опытных работ, позволили сократить время нанесения песка и печати одного слоя до 20 с, что обеспечивает рост 7,2 см/ч. Мы предпочитаем говорить именно об абсолютной скорости роста по вертикальной оси, поскольку объем построения зависит от горизонтальных размеров самой камеры. Так, для одной и той же вертикальной скорости, скажем 7,2 см/ч, получаются различные значения для камер с разными горизонтальными размерами (X, Y) 300×500 мм и 700×700 мм. Значения объемов построения в этом случае будут 10 800 и 35 200 см3/ч соответственно. При еще больших размерах камер получаются еще большие значения объемов при равной вертикальной скорости роста. Таким образом, к 2018 году увидела свет обновленная установка АТ300 с прежними линейными размерами 500×300×300 мм (X, Y, Z), но значительно (более чем в два раза) ускоренная, обладающая скоростью построения 7,2 см/ч, или, другими словами, 10 800 см3/ч.
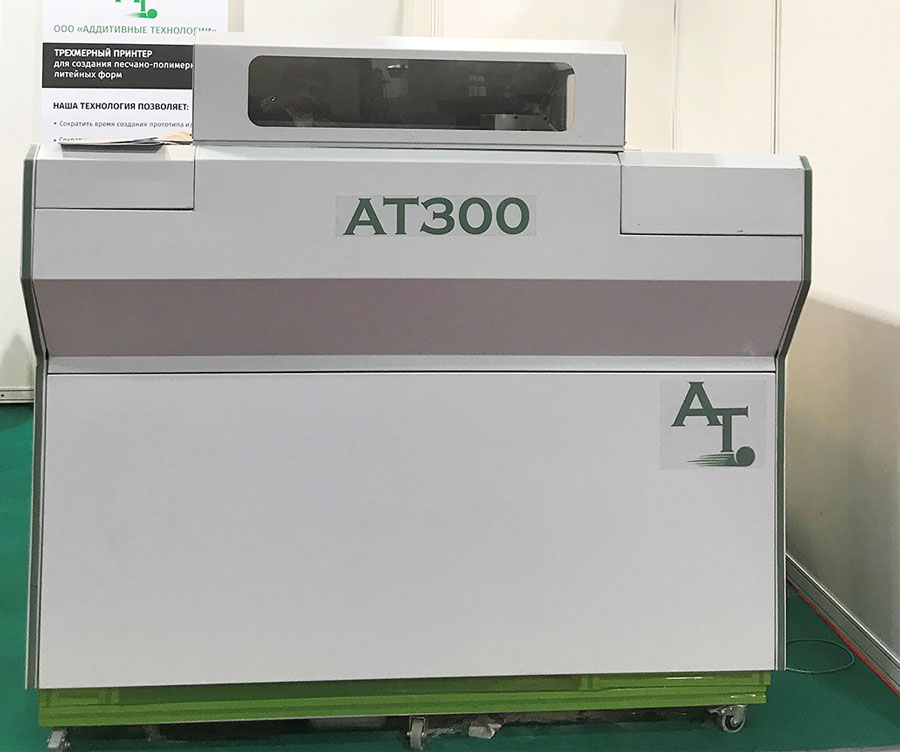
Рис. 4. Установка АТ300
Параллельно с усовершенствованием АТ300 велась работа по созданию принципиально новой установки АТ700, в основе действия которой лежат те же принципы, что и у АТ300, однако она имеет ряд коренных отличий от младшей модели. Во-первых, АТ700 оснащена системой автоматической подачи песка. Если АТ300 предполагает ручную засыпку песка в бункер построения после предварительного ручного смешивания с катализатором, то в АТ 700 песок подается автоматически в бункер замеса, где происходит впрыскивание катализатора и размешивание его в массе песка. Затем песок из бункера замеса автоматически подается в рабочий портал, который, двигаясь в горизонтальном направлении, обеспечивает послойное нанесение песка. Данный процесс повторяется по мере того, как заканчивается песок.
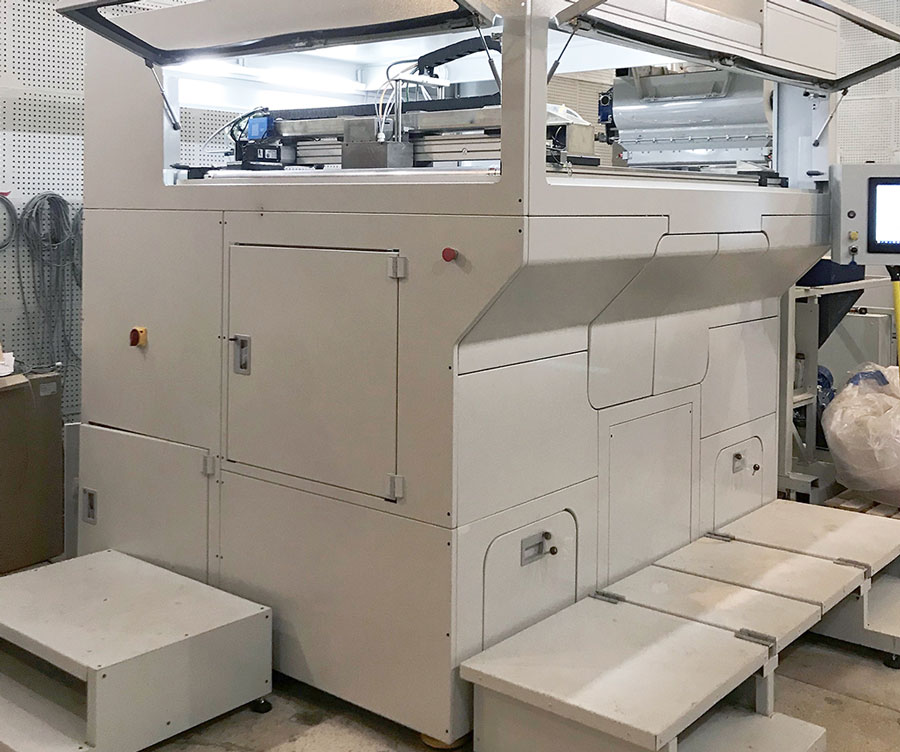
Рис. 5. Установка АТ700
Второе существенное отличие — АТ700 предполагает сменный бункер построения. После окончания цикла печати бункер, в котором проводилось построение форм, можно выкатить, открыв боковые дверцы, а вместо него поставить пустой бункер и начать следующий цикл печати. Пока машина строит очередную партию форм, можно заняться выемкой и очисткой уже построенных изделий. Такая технология значительно экономит время и позволяет печатать формы практически непрерывно. Третьим отличием установки АТ700 является оснащенность четырьмя головками (у АТ300 — одна) и измененная версия системы управления печатью. АТ700 обеспечивает вертикальную скорость печати 7,2 см/ч, что соответствует 35200 см3/ч.
Четвертое — процесс печати на АТ700 полностью автоматизирован. На входе имеется STL-файл, загружаемый в компьютер принтера. Далее автоматика разбивает файл на слои, подает их на систему управления, определяет необходимое количество катализатора и смолы, время замеса песка и оптимизирует процесс построения. Управление принтером осуществляется как с выносной консоли принтера, так и по удаленному доступу через Wi-Fi.
Таким образом, по техническим характеристикам АТ700 становится серьезным конкурентом западным образцам подобного оборудования (уже упомянутым VoxelJet и ExOne). При этом наши принтеры на 90% состоят из российских комплектующих, что делает их стоимость в несколько раз ниже импортных аналогов, а использование отечественных расходных материалов позволяет добиться себестоимости форм в пределах 100 рублей за 1 кг или даже меньше при условии оптимальной заполняемости камеры построения.
В качестве примера можно привести тендер 2018 года на производство и поставку песчано-полимерного принтера для Магнитогорского металлургического комбината. Помимо ООО «Аддитивные технологии» в отборе принимали участие дистрибьютор зарубежной компании VoxelJet, а также несколько компаний, продвигающих на рынке технологию печати литейных форм из плакированного песка. На первом этапе тендера проходил выбор технологии путем сравнения основных параметров: скорости построения и себестоимости форм. Поскольку технология спекания плакированного песка отстает по скорости построения от песчано-полимерной технологии более чем в 10 раз, а стоимость 1 тонны плакированного песка почти в 30 раз дороже стоимости песка, применимого для BJ, то выбор естественным образом пал на технологию послойной полимеризации, лежащую в основе отечественных принтеров. Сравнение остальных технико-экономических параметров привело к выбору компании «Аддитивные технологии» в качестве победителя тендера.
В настоящее время линейка принтеров для производства песчано-полимерных форм от компании ООО «Аддитивные технологии» насчитывает четыре модели: АТ300, АТ700, АТ1000 и АТ2000. Номер коррелируют с размером камер построения: модель АТ300 имеет размеры (X, Y, Z) 500×300×300 мм, модель АТ700 — 700×700×450 мм, модель АТ1000 — 1000×1000×450 мм, модель АТ2000 — 2000×(1000–2000)×700 мм. Все модели имеют примерно одинаковую скорость построения по вертикали, колеблющуюся в пределах 7–9 см/ч, что обеспечивает объем построения до 250 000 см3/ч у старших моделей.
Маркетинговое исследование ведущих компаний (консультации с главными технологами, директорами по инновационному развитию, техническими директорами), имеющих постоянную потребность в литье, позволило сделать вывод, что многие предприятия проводят реконструкцию литейного производства, ориентируясь на новые технологические процессы, материалы и перспективное оборудование. Основная цель реконструкции — расширение объемов производства, повышение качества изделий, отвечающих современным требованиям заказчика, снижение сроков изготовления и себестоимости продукции, а также улучшение экологической ситуации и условий труда.
С учетом активного технического перевооружения промышленности (общий объем программ на предприятиях ОПК превышает 1 трлн рублей) и внешнеполитических процессов предполагается высокий спрос на отечественные технологии и сырьевую базу. Ожидается наличие спроса и со стороны малых предприятий, ориентирующихся на мелкосерийное производство литьевых изделий, а также инжиниринговых компаний, занимающихся разработкой конструкций литьевых изделий и литьевой оснастки. Предлагаемые аддитивные технологии позволяют потенциальным пользователям сократить издержки и сроки разработки изделий.

Антон Шаронов, главный технолог, компания «Диполь»
В условиях активного развития аддитивных технологий в мире можно выделить тенденцию внедрения 3D-принтеров в сектор индивидуальных, узкоспециализированых машин. На этом фоне особенно выигрышно выглядят принтеры для получения песчано-полимерных форм. Их востребованность связана с тем, что в мировой металлургии неизменно присутствует сегмент производства изделий небольшим тиражом (опытные партии, отработка технологий, проверки проектирования — эти случаи предполагают изготовление одного или нескольких изделий). Надо отметить, что производство и проектирование оснастки при выпуске тиражом до 50 единиц почти никогда не окупали своей стоимости, но с появлением аддитивных технологий решение подобных «единичных» задач перестало быть убыточным, а скорость исполнения проектов выросла в разы. Не секрет, что выпуск металлического изделия по стандартной технологии на современном отечественном предприятии занимает более шести месяцев. С внедрением в технологический процесс 3D-принтеров эти сроки сократились до двух-трех недель.
Сегодня принтеры для получения песчано-полимерных форм изготавливаются во многих странах мира. Первенство принадлежит немецким производителям ExOne и Voxeljet. Изначально это была одна компания, по замыслу руководства разделенная на две: первая должна была заниматься оборудованием для получения песчано-полимерных форм, вторая ориентировалась на технологии для выплавляемых моделей. Что характерно, в итоге обе в настоящее время работают в одном сегменте. Использование оборудования данных производителей на территории России связано с рядом сложностей. И хотя проблема применения российских материалов в этих машинах многими предприятиями уже решена, но по-прежнему остро стоит вопрос стоимости запчастей и сервисного фирменного обслуживания, которое в нашей стране попросту не налажено. В этой ситуации тем более следует обратить внимание на отечественные разработки или предложения юго-восточных производителей. Выбор оборудования и представителей растет очень быстро. И уже скоро отзывы специалистов и пользователей помогут сформировать объективное мнение о качестве и возможностях таких машин. Пока же можно с уверенностью заключить, что все крупные предприятия отрасли рассматривают возможности использования 3D-принтеров для получения песчано-полимерных форм в своих металлургических и литейных цехах.